Catalytic Oxidizers
Low-Temperature VOC Destruction with High Efficiency
When volatile organic compounds (VOCs) are present at lower concentrations, catalytic oxidizers offer a powerful and energy-efficient solution. By leveraging specialized catalysts, these systems significantly reduce the combustion temperature—often down to 500–600°F (260–315°C)—which leads to lower operating costs and less fuel usage compared to direct thermal oxidation.
Why Choose Catalytic Oxidizers?
Catalytic oxidation is a proven method for treating air streams with VOC concentrations below 2,500 ppm. These systems convert harmful organics into harmless byproducts like CO₂ and water vapor, without requiring the high temperatures associated with traditional oxidizers.
Key Benefits:
- Lower Operating Temperatures: Reduced fuel costs thanks to efficient catalytic combustion.
- NOₓ-Free Destruction: Special catalysts can destroy ammonia and other nitrogen compounds without generating nitrogen oxides.
- Compact System Footprint: Ideal for facilities with limited space or moderate flow rates.
- Flexible Configurations: Horizontal or vertical designs to match your system layout.
- Reliable Emissions Control: Guaranteed destruction efficiency with proven performance.
How Catalytic Oxidizers Work
Catalytic oxidizers use a gas burner to preheat the process stream. As the gas passes through a catalyst bed, chemical reactions occur that oxidize VOCs into benign compounds at lower temperatures than traditional thermal oxidizers.
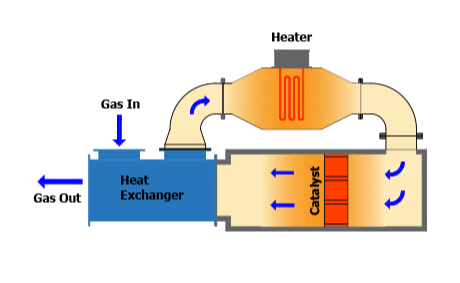
System Components:
- Burner Unit: Provides supplemental heat as needed to reach catalyst activation temperature.
- Catalyst Chamber: Where the oxidation reaction occurs; designed to maximize residence time and efficiency.
- Heat Recovery: Optional air-to-air heat exchangers improve energy efficiency by preheating incoming air.
Optional Features
- Air-to-air heat exchangers for enhanced energy recovery
- Tail gas treatment systems
- UL, FM, or other certified safety components
Common Applications
Catalytic oxidizers are best suited for operations with:
- Low VOC concentrations
- Ammonia or nitrogen-containing gases
- Need for energy efficiency
- Desire to avoid NOₓ emissions
Key Features of MXD Catalytic Oxidizers
At Branch Environmental, our catalytic oxidation systems are built to perform with precision and longevity. Every unit is engineered with your process goals in mind.
-
Guaranteed Destruction Efficiency
Each system is performance-guaranteed to meet your target VOC removal rates, even at lower operating temperatures.
-
Vertical & Horizontal Designs
Our oxidizers are available in both vertical and horizontal configurations to integrate seamlessly into your facility layout.
-
Capacities up to 25,000 CFM
Shop-fabricated units can handle flows up to 25,000 CFM, with larger options available via field fabrication.
-
Tail Gas Treatment Options
For added emissions control, we offer integrated tail gas scrubbers or other post-treatment systems as needed.
-
Complete System Packages
We deliver turnkey packages that include the oxidizer, burner, controls, fans, pumps, and optional heat recovery systems.
-
Corrosion-Resistant Construction
Catalytic oxidizers can be built from a wide range of materials including stainless steel, fiberglass, and specialty alloys to suit corrosive or high-moisture environments.
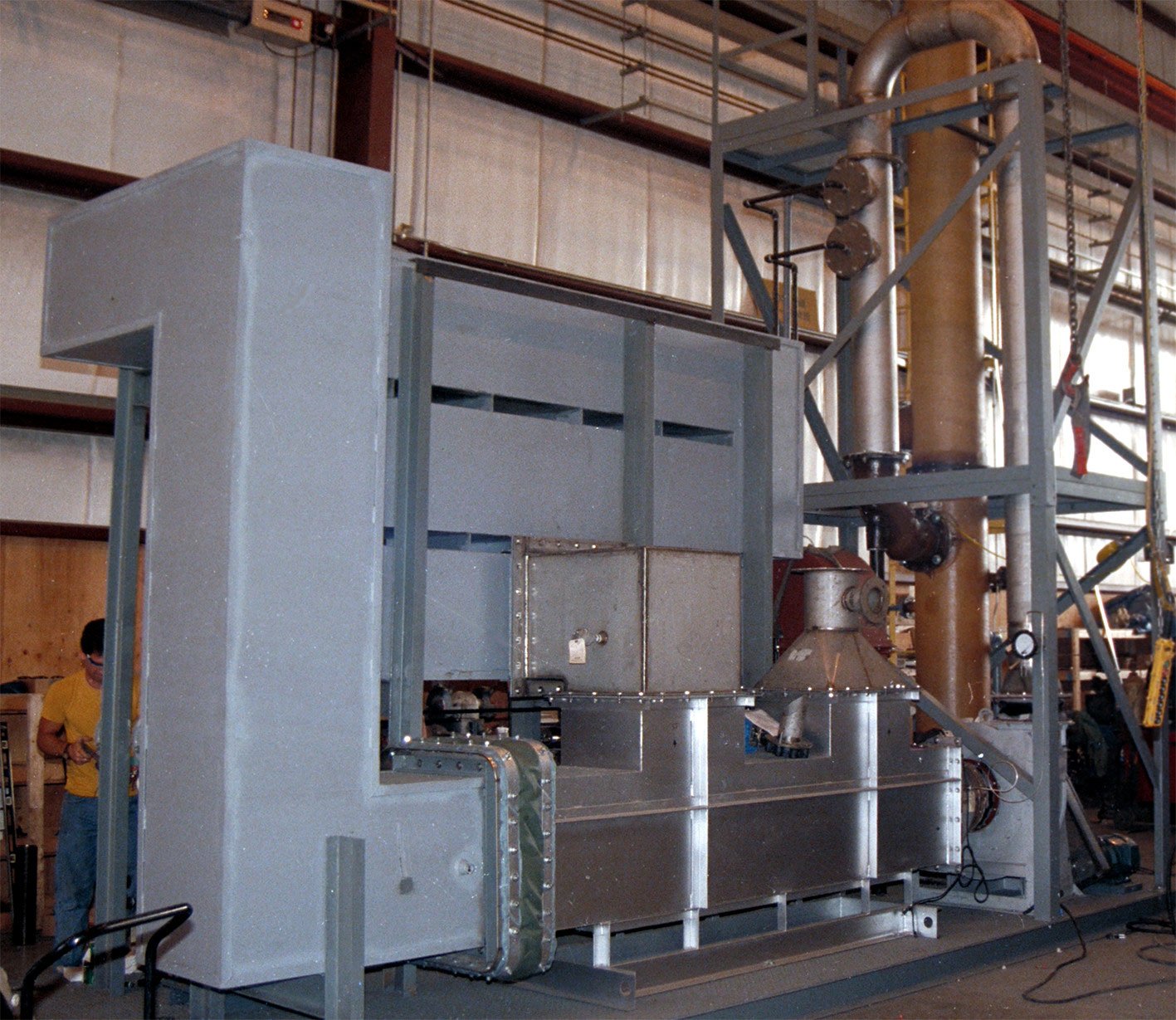
At Branch Environmental, we custom design and engineer systems with your goals in mind.
Guaranteed Performance Tailored To Your Application
Various Material Options For Any Operating Condition
Complete Packages Including: Controls, Fans, Pumps & More
Scalable Designs To Fit Your Manufacturing Needs
Let's Work Together
We don’t just offer catalytic oxidizers—we deliver complete air pollution control systems tailored to your requirements. Whether you’re targeting low-VOC air streams, minimizing NOₓ, or improving your energy efficiency, our team is here to help.